Bus Bar Solutions
Power distribution has become very critical and due to higher power densities, optimal designing of power distribution is the need of the hour and often must meet rigorous environmental challenges: high shock and vibration, extreme temperatures and high humidity. Incresol has developed core design expertise in power distribution solutions and we work with you to design a power interface solution that maximizes power efficiencies while eliminating often cumbersome cabling.
As the leader in the world of power distribution solutions, Incresol busbars main differentiators are superb quality and reliability, electrical and mechanical expertise, co-engineering and flexible lead times
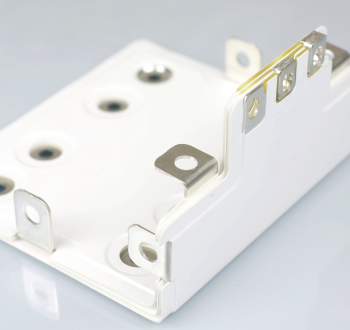
capabilities
- Project Management
- Design & Engineering
- Manufacturing
- Test
WHY INCRESOL?
SUPERIOR QUALITY FROM DESIGN THROUGH MANUFACTURE.
Why choose our products?
From the first design consultation through the final shipping, Incresol provides customers with innovative power distribution solutions being cost effective without compromising on the quality.
Properly selected insulation
Properly selected insulation is the key to bus bars electrical performance and we at Incresol take special care in choosing the insulation. We use a wide variety of dielectric materials like Mylar, PEN, Nomex, FR4, GPO, Kapton etc., based on the application requirements. In addition to sheet lamination we have the capability of building bus bars with powder coated insulation and plastic molding which provides high dielectric protection to bus bars to be used in harsh environment.
Precise processing of di-electric components
Precise processing of di-electric components is very important in manufacturing laminated bus bars. To ensure quality, we maintain calibrated humidity and temperature controlled conditions to store our insulation. Precision steel rule dies are used for cutting the insulation, ensuring uniformity of size to produce quality bus bars.
Assembly and lamination
Assembly and lamination is controlled using sophisticated lamination systems and tools specially designed and manufactured for each bus bar. Hardware and interconnection devices can be added before or after the lamination and plating process.
Electrical testing
Electrical testing plays a key role in the bus bar performance and Incresol conducts 100% HI-Pot testing of the bus bars ensuring the dielectric material used performs as per the specification. Partial discharge is performed based on customer requirement
BUS BAR SOLUTIONS OVERVIEW
LAMINATED
BUS BAR
Custom engineered to fit customer space constraints with specific electrical benefits including low inductance, minimal voltage drop and specified partial discharge level. Incresol multi conductor bus bar comes in various conducting materials, insulations and plating options, including those suitable for defense and aerospace environments.
FLEXIBLE
BUS BAR
Flexible busbar with pure copper laminates within protective PVC insulations offers flexibility at connection points to make application more pliable. With benefits like easy and quick bending, design flexibility, these bus bars can be used in critical application like battery module connections of EV, interconnect in drive systems and power supplies.
POWDER COATED
BUS BAR
Powder coated bus bars have unique advantages compared to any other type of insulation. These are cost effective compared to film insulation and can be easily applied to any shape and size using electrostatic spray process or dip process. Epoxy coating powder offers very high dielectric strength and it will bond directly to the bus bar.
MOLDED
BUS BAR
Incresol insert molded solution for power distribution applications can offer customers with customized solution. With key features like integration of electronic components such connectors, sensors etc can offer customers with plug and play solution. Designs can meet stringent environmental demands, such as extreme temperature, fluid exposure and vibration. Another major benefit is the reduction of electrical connections, which improves overall reliability.
Market &
Application
INDUSTRIAL
- Motor drives
- Motor controls
- Welding equipment
- Elevator systems
AEROSPACE AND SPACE
- Satellite systems
- Aircraft
- Space stations
- Missile systems
MEDICAL AND DIAGNOSTIC EQUIPMENT
- MRI
- CAT Scan
TRANSPORTATION
- Mass transit
- Hybrid vehicles
- Electric vehicles
- Earthmovers
- Light rail systems
POWER CONVERSION
- Power supplies
- UPS systems
- Inverters